
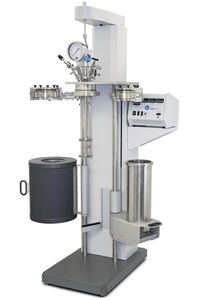
Reactor for solvent-free polymer processingĬonverting the polymer industry to solvent-free polymerisation processes and avoiding unnecessary recirculation decreases energy consumption and reduces waste production. At higher conversion and/or molecular weight, the reaction mass will become very viscous, which limits the ability of conventional reactor technology to provide adequate mixing, minimize mass transfer effects on reaction kinetics, remove exothermic heat of reaction and ensure proper heat transfer in order to eliminate hotspots/thermal degradation. Polymerization of lactide to polylactic acid (PLA) can be performed using conventional reactor technology such as stirred tank reactors, but the conversion and/or final molecular weight may have to be controlled to a lower level. Modeling and simulatio of poymerization of lactide to polylactic acid and co-polymers of polylactic acid using high viscosity Kneader Reactors One such effort has yielded extremely promising results. The time and cost involved in removing and treating solvents in th e final stages of production, for example, were acceptable, but as pressure builds on manufacturers to reduce operating costs, there is greater urgency to develop processes that can help streamline cost and production. One such effort by List AG has yielded promising results.Ĭonventional polymerisation in the production of elastomers has been the norm for decades. But as pressure builds on manufacturers to reduce operating costs, there is greater urgency to develop processes that can help streamline cost and production. The time and cost involved in removing and treating solvents in the final stages of production, for example, were acceptable. One such effort has yielded extremely promising results.Įfficient and eco-friendly polymerization of elastomersįor decades, conventional polymerization in the production of elastomers has been the norm. Yet as pressure builds on manufacturers to reduce operating costs, there is greater urgency to develop processes that can help streamline costs and production techniques. The time and cost involved in removing and treating solvents in the final stages of production were acceptable. Nun liefert ein innovativer Ansatz aus der Schweiz, die sogenannte Direct Devolatilization (direkte Entgasung) von Polymerlösungen, vielversprechende Ergebnisse.ĭirect devolatilisation in a closed systemįor decades, conventional polymerisation has been the norm in the production of elastomers. Gefragt sind intensivierte Prozesse, die unnötige Verfahrensschritte ersparen und sowohl Zeitaufwand wie auch Kosten senken. The timestamp is only as accurate as the clock in the camera, and it may be completely wrong.Der zunehmende Kostendruck macht keinen Halt vor der Produktion von Elastomeren. If the file has been modified from its original state, some details such as the timestamp may not fully reflect those of the original file.
#HERSTELLER VON REAKTOR SOFTWARE#
This file contains additional information such as Exif metadata which may have been added by the digital camera, scanner, or software program used to create or digitize it.
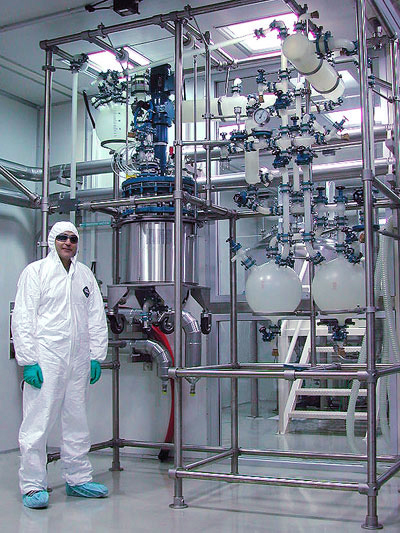
#HERSTELLER VON REAKTOR LICENSE#
GFDL GNU Free Documentation License true true A copy of the license is included in the section entitled GNU Free Documentation License. Permission is granted to copy, distribute and/or modify this document under the terms of the GNU Free Documentation License, Version 1.2 or any later version published by the Free Software Foundation with no Invariant Sections, no Front-Cover Texts, and no Back-Cover Texts. CC BY-SA 3.0 Creative Commons Attribution-Share Alike 3.0 true true share alike – If you remix, transform, or build upon the material, you must distribute your contributions under the same or compatible license as the original.You may do so in any reasonable manner, but not in any way that suggests the licensor endorses you or your use. attribution – You must give appropriate credit, provide a link to the license, and indicate if changes were made.to share – to copy, distribute and transmit the work.
